中国半导体照明网专稿:近十几年来LED芯片切割技术的进步可说是一日千里:从钻石刀切割(Diamond scriber)技术到激光切割技术,再到前几年且正火红的隐形切割SD(Stealth dicing)切割技术。2009年日本Disco的隐形切割技术标榜着可以维持与原有制程方法同等的亮度,同时还能提升产能及合格率的优势进入LED切割市场,是切割技术的一大跃进。SD切割所使用的激光脉冲宽度时间为10-13秒,属于飞秒激光(Femtosecond),而相较于SD激光,表面激光属于长脉冲激光,与SD切割激光之不同点在于其加工中会有较多的热效应产生。
本文在分析几种不同切割技术的基础上,集中介绍了有助于提升LED芯片产能的隐形切割(SD)技术。
一、几种不同切割技术的优劣
近年来在隐形切割(Stealth Dicing,SD)的基础上已发展出一些的激光切割专利;如芯片内部双切割道切割专利[1]。双切割道切割主要是解决芯片厚度变厚问题,其原理是使用一种双聚焦(a plurality of focal points)的切割光学机构,可一次同时切割出二道切割痕迹,降低切割时间。
再者,为增加裂片的准确性,所以有多切割道切割的技术专利产生[2],此切割技术会因第一道切割道的内应力破裂而产生沿芯片厚度方向的弯曲,此弯曲量会影响第二道切割的聚焦点,导致多条切割道的变质层不在同一劈裂线上,影响裂片的准确性。为改善此不良现象,专利[3]提出锯齿状切割技术。
锯齿状切割技术示意图如图1所示,切割技术原理是使用同一波长(1064 nm)激光光源及不同激光能量(0.92、0.8、0.4 W),其它激光切割条件参数完全相同;并分别进行M1、M3、M2等三道切割道切割及沿蓝宝石基板六面体晶体结构的C-plane方向产生斜裂痕迹a及b,而将M1~M3切割道连接起来,形成沿着切割道5的断裂面,裂开编号1的工件。当芯片放在蓝膜上时,芯片会因蓝膜上的扩张而自动裂开,产生一颗颗的芯片。
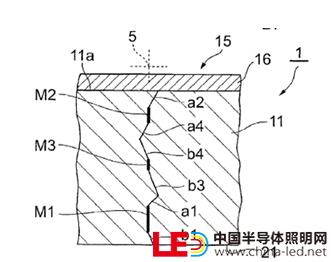
图1 锯齿状切割技术示意图
由于芯片厚度的变厚,及为了能够降低切割时间及提升劈片合格率,所以双切割技术现已熟用在芯片的切割制程上,但对于芯片厚度在90~110μm的切割制程,单切割道技术还是较适合。
拥有这些切割技术并不保证芯片在市场上的竞争优势,然而能善用这些技术,芯片才会有市场竞争优势。当激光切割技术出现时,LED制造厂不满意于芯片的产出亮度,所以就需要找出解决去除破坏层的方法;同样地,当SD切割技术被使用时,LED制造商为了能够降低芯片制造成本,而往单片的芯片产出增加以降低机台的使用成本考虑。
二、隐形切割技术主要内容
就如前言所示,激光切割会产生切割道侧壁的破坏物,严重影响出光效率。所以需要去除这些破坏物。因为激光切割是利用加工对象的表面吸收激光的高能量造成烧结的加工方式。如图2左图所示,图2右图为激光烧结痕迹。
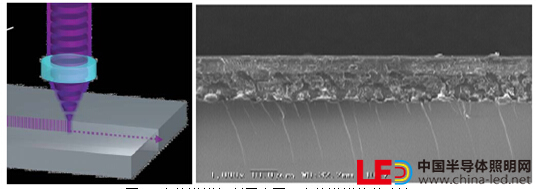
图2 左为激光切割示意图;右为激光烧结痕迹
这片破坏层严重影响芯片侧壁出光,所以需要使用化学溶液(硫酸加磷酸混合)以湿蚀刻方式去除。进行湿蚀刻时发现一个有趣的现象,就是切割道开口的大小会影响破坏层去除的干净程度。参考图3,左图切割道开口宽度为7~8μm;而右图为11~12μm。同一款芯片进行相同湿蚀刻时间后的亮度比较,如图4所示。从图4中可知切割道开口宽度较宽的亮度比较亮;并且统计不同外延片生产批次的亮度平均值差为0.9~1.6%,如表1所示。
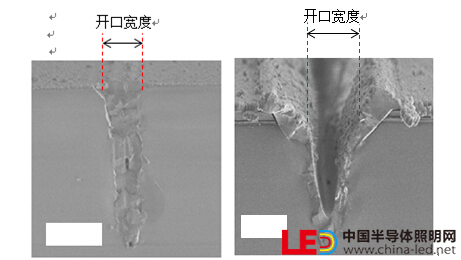
图3 左图切割道开口宽度7~8μm 右图切割道开口宽度11~12μm
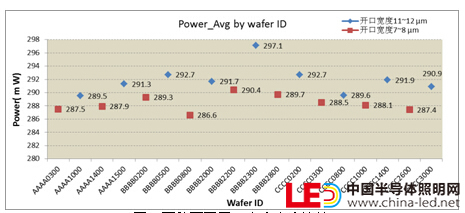
图4 两种不同开口宽度亮度比较
表1 不同外延片生产批的亮度平均值差(%)
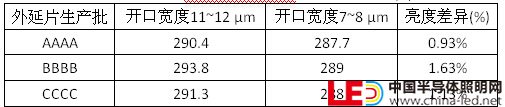
将开口宽度7~8μm的切深适当变浅[4],开口宽度11~12μm的切深不变;进行不同外延片亮度等级(E1~E4)的同一款芯片的相同LBR(Laser By-product Removal)制程条件后的亮度比较,结果如图5所示;二者的平均亮度分别为306.75 mW及307.25 mW,已非常接近,相差在0.5%内。
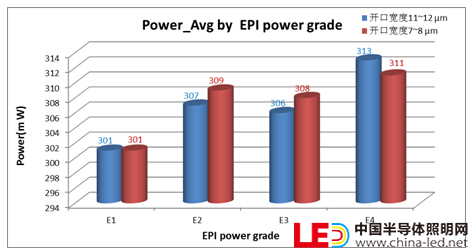
图5 开口宽度7~8μm的变浅切深与开口宽度11~12μm的原切深亮度比较
由于找到切深适当变浅的方法,使原来停用的切割道开口小的切割机台又可开始生产,不需要再额外购买机台以满足因机台不足的产能缺口,所以机台投入生产可省下的费用计算如下:
机台的成本摊提/每月-操作人员费用/每月=机台省下的费用/每月
其中机台的成本包含机台售价及保修成本。若机台价格=240万RMB/台,机台保修成本=27万RMB/台,以8年来计算摊提,则每月机台费用需摊提=2.8万RMB/台,若每月人力费用=0.3万RMB,则每月可省下费用=2.8-0.3=2.5万RMB/台。
芯片切割走道宽度若从40μm缩小到30μm,使用SD技术所面临的问题将是芯片劈裂后容易裂到芯片正面Mesa(高台)附近或是伤到Mesa。
SD切割也是使用激光光源,其激光聚焦点是在加工件内部。利用工件内部吸收激光能量之物质现象,使内部材质变质而产生裂痕,内部破裂痕往两侧横断面延伸成破裂面,此破裂面产生我们称为预裂现象为内部变质层的体积膨胀应力及热应力释放,使得变质层到两侧表面间产生裂痕后,再于激光入射反方向进行劈裂分晶[5],如图6所示。图6左图为SD切割激光聚焦在工件内部的示意图;右图为SD切割后的横断面切割痕迹示意图。
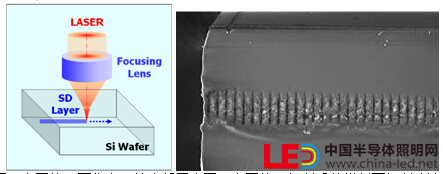
图6 左图为SD聚焦在工件内部示意图;右图为SD切割后的横断面切割痕迹
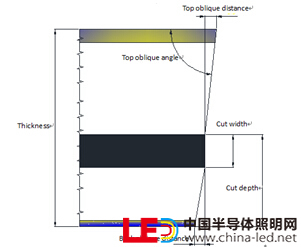
图7 SD切割劈裂后芯片正-背面斜裂示意图
芯片经SD切割及劈裂机劈裂后在正面会产生斜裂现象如图7所示。虽然激光光从芯片背面的入射位置可调整在芯片的走道中间位置,但实际上芯片在劈裂后却是会产生正面斜裂,且在相同的切深及切宽下芯片厚度越厚斜裂会越严重。为要了解并解决这种异常现象,需要从了解蓝宝石衬底的材料结构开始。因为蓝宝石衬底之化学成份为氧化铝单晶(Single Crystal Sapphire,Al2O3),结构中之氧原子以接近最密六方堆积(HCP,Hexagonal Closed Packed)之排列方式排列;主要的晶面有C面(0001)、A面(1120)及R面(1102)等[6],示意图如图8左图所示。
C面(0001)的蓝宝石单晶普遍的被用来作为发光二极管新型半导体氮化镓系列的基板材料[7],A面为一般的正常切割劈裂面(不会产生斜裂面),而R面则会造成劈裂斜裂的面。参考图8右图,若LED芯片是使用蓝宝石基板C面生长磊晶层,若设定A面为X轴方向(与X轴平行)及R面为Y轴方向(与Y轴平行)但与Y轴轴向面会有固定角度差。SD切割的内部结构改质层皆在A面及R面上,产生的破裂面也会顺着A面及R面往两侧表面延伸。因为R面与Y轴轴向面有角度差,当破裂面会顺着R面裂至Y轴正面走道,裂痕会偏一边;而A面与X轴轴向平行,无角度差,所以X轴裂痕不易偏一边,这就是为什么SD切割劈裂后芯片正面Y轴会斜裂的原因。但若设定A面为Y轴方向(与Y轴平行)及R面为X轴方向(与X轴平行),则正好相反, X轴正面走道裂痕会偏一边而Y轴裂痕不易偏一边。
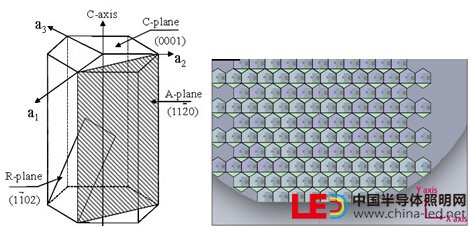
图8 左图为蓝宝石衬底的C面,A面,R面示意图;右图为LED芯片示意图
有些切割工程人员想从斜裂方向的一致性来进行改善,例如: 若芯片正面斜裂在同一方向且斜裂的距离固定,那就可以微调激光切割位置使劈裂后正面斜裂痕迹在接近芯片走道中间位置。但由于不同衬底的供应厂在R面的排列方式不尽相同,因为不同基板供应厂提供的基板R面方向会不一样,这会造成芯片劈裂后斜裂的方向不一致。所以无法从固定斜裂的方向来改善芯片正面斜裂的问题,除非每家基板供货商的R面排列方式都是一样的且是有卡规格的。直接解决此一斜裂问题的方法就是使切割位置越靠近芯片正面越好,这会减少芯片正面斜裂的距离(Top oblique distance,参考图7)而避开斜裂到芯片正面mesa区域。但这样做也会有风险,因为越接近芯片正面,激光光有可能伤到磊晶层而造成光电性信赖性失效,所以激光切深到底可以多深,一方面是要看磊晶层的强度,一方面则需要工程人员进行实验测试以找出最适合的SD切割深度。
举例而言,若芯片厚度为150μm,走道宽度30μm,斜裂离mesa距离在6~8μm之间,则切割深度预估是多少μm? 欲解决此一问题,首先可以先使用图7的斜裂角度(Top oblique angle)预估切深并设定斜裂离mesa距离为7μm,由于此斜裂角度接近固定值,依此固定值粗估计算切深约为74μm左右,使用此预估切深进行制程实验以找出实际合适的切深值。
若切割走道从30μm缩小为20μm除再次面临芯片正面斜裂的问题外,同时也面临其它困难点。对于劈裂后斜裂的问题改善,现阶段唯一的方法就是加深切割深度,但须考虑激光光不能太靠近芯片正面以避免造成芯片微漏电流的异常现象。
针对同一款芯片尺寸在相同的发光区面积下将切割走道从40μm缩小到30μm及再缩小为20μm后,单片芯片增加的芯片颗数比较表如表2所示。切割走道从40μm缩小到20μm,则芯片产出增加约10.30%,大大降低芯片制造成本。
表2 芯片切割走道从40μm缩小到20μm单片芯片增加的芯片颗数(%)
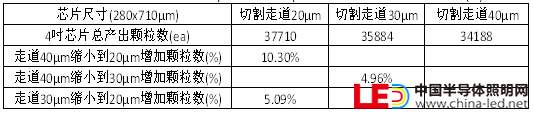
探讨厚度150μm及切割走道宽度20μm的芯片如何进行切割才不会伤到mesa?最直接的想法就是切割深度尽量靠近芯片正面以避免正面斜裂伤到mesa。但这会产生较严重的背面斜裂(back oblique distance),如图9左图,较严重的背面斜裂容易造成芯片封装固晶胶量无法判断是否足够而降低固晶效率。为了避免产生这类的异常,可以进行双切割,如图9右图所示。双切割的一道切割靠近正面,其余另一道切割就会较靠近背面而降低背面斜裂。
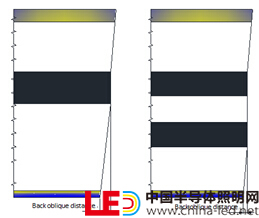
图9 左图为单切割道 右图为双切割道
但芯片进行双切割若是一道一道的切割,则切割效率会降低许多,且由于是双切痕所以出光效率也会受影响。SD厂商提供了一次切割产生二道切痕的技术;在相同激光功率下,激光分成二个聚焦点,分别聚焦在工件内部进行切割。根据切割工程人员所提供的数据得知,应用一次切割产生二道切痕的技术所增加的产能比一道一道的切割约多出30%以上。再者,双切痕的优点为可增加芯片裂片的容易性,劈片合格率稳定,较不会发生劈不断的异常情形。虽然有以上的优点,但是由于是双切痕,容易令人产生芯片光输出变低的印象,所以需要进行验证。
将同一款芯片进行不同切割方式后的封测亮度(Power, mW)比较,以一道切割产生一道切痕的双切痕切割方式作为比较基准,在相同芯片波段下的比较结果如下表3所示。由表3得知同一款芯片在不同的MOCVD机台下的二种切割方式的亮度(Power, mW)差异值<1%,非常接近,这是由于双切痕的激光功率与单切痕的一样,只是一分为二。
表3 同一款芯片在相同波段不同MO机台下的亮度比较

三、结语
SD切割技术在未来几年将是芯片切割技术发展的主流,因为它带来LED芯片切割技术的多变性;从搭配机台参数的排列组合的变化开始、到芯片内部可进行不同切割位置的交叉使用、再加上对于蓝宝石基板C-plane的熟悉应用,可说是将整个SD切割技术发挥的淋漓尽致。不仅如此,切割道逐渐缩小,单一芯片的芯片产出量变多,芯片制造成本逐季下降,同时芯片的光、电性能也逐季提升,为LED芯片能满足市场产品的性能及价格需求,加快LED芯片使用的普及化。LED芯片未来将大量被使用在UV照明,产生净化空气、环境保护的作用;使用在智能照明,产生节能减碳的作用;对人类社会、生态环境保护是一项卓越的贡献。
参考文献
[1].Keiji Nomaru, Tokyo(JP), LASER BEAM PROCESSING MACHINE, US 7,402,773 B2, Jul. 22, 2008.
[2].Ryuji Sugiura, Hamamatsu(JP),Takeshi Sakamoto, Hamamatsu(JP),LASER PROCESSING METHOD AND CHIP, US 7,897,487 B2, Mar. 1, 2011.
[3].Takeshi Sakampoto, Hamamatsu(JP),LASER WORKING METHOD, US 8,431,467 B2, Apr.30,2013.
[4].Chih-Hui Alston Liu, Manufacturing method of a light-emitting device, US 20130196461 A1, Aug.01, 2013.
[5].HAMAMATSU : Stealth Dicing Technical Information for MEMS. http://jp.hamamatsu.com/resources/products/etd/pdf/SD_tech_forMEMS_TLAS9005E02.pdf
[6].H. Amano , K. Hiramatsu, and I. Akasaki, Jpn. J. Appl. Phys. 27, L1384 (1988).
[7].S. Nakamura, T. Mukai, and M. Senoh, Appl. Phys. Lett. 64, 1687 (1994).
本文来源于电子信息产业发展基金项目:室内半导体照明器件、电光源产品与检测技术研发及应用 财建【2013】757号